Temperature Measurement
Temperature is the world’s most commonly measured physical parameter, and Gantner Instruments is the most stable and accurate data acquisition supplier for temperature measurements. Temperature is generally measured using industrial temperature sensors such as temperature probes (e.g., thermocouples, RTD temperature sensors like Pt100/Pt1000), thermistors (NTC), infrared (IR) temperature sensors, or other application-specific transducers.
Measurement methods should be selected carefully based on several critical factors: the required temperature range, response time, accuracy, and cost, as well as environmental considerations such as high-voltage potentials in battery testing or severe electromagnetic interference from electric motors or inverter-driven systems. Each of these conditions can significantly impact measurement stability and accuracy, making proper sensor selection and DAQ essential.
Measuring temperature accurately in engineering projects can be more complicated than it first appears. Many engineers encounter similar challenges when integrating industrial temperature sensors into test setups or industrial systems. Here we address some of the most common issues – and how to overcome them – in practical temperature measurement. We’ll also highlight how Gantner Instruments’ tools and expertise can help you get reliable results.
High-precision thermocouple measurement with cold junction compensation (CJC)
Optimized for Type K temperature probes
For thin TC wires or noisy environments
RTD temperature sensor (Pt100/Pt1000) and NTC thermistor measurement module
Specialized for low-current for cryogenic measurements
NTC measurement module for extended resistance ranges
Thermocouple measurement module for high-voltage environments and Customized connector like Spring terminals, Lemo Redel, Thermosensor
High-voltage RTD and/or NTC measurement module
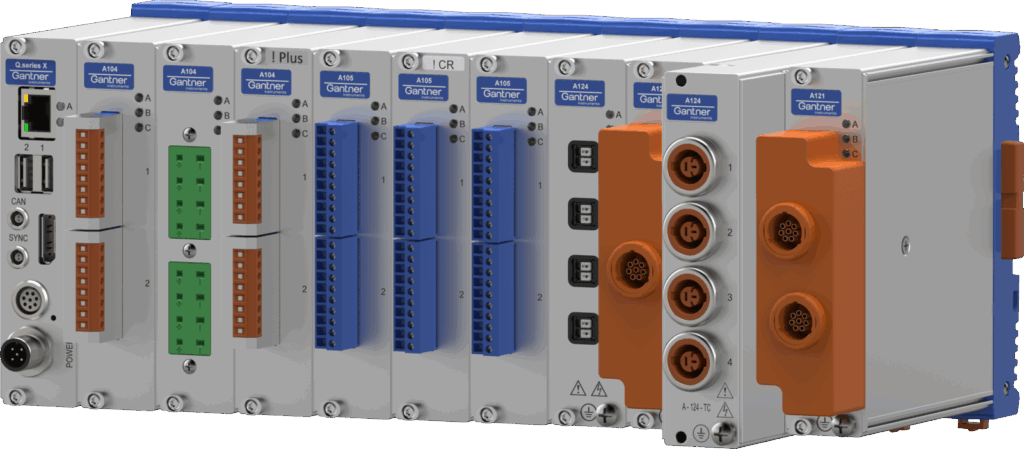
Selecting the Right Sensor for Your Needs
“Should I use a thermocouple, RTD, thermistor, or infrared (IR) temperature sensor?” – This is often the first question.
Choosing the right industrial temperature sensors significantly affects your measurement accuracy and reliability:
Selecting the Right Sensor for Your Needs
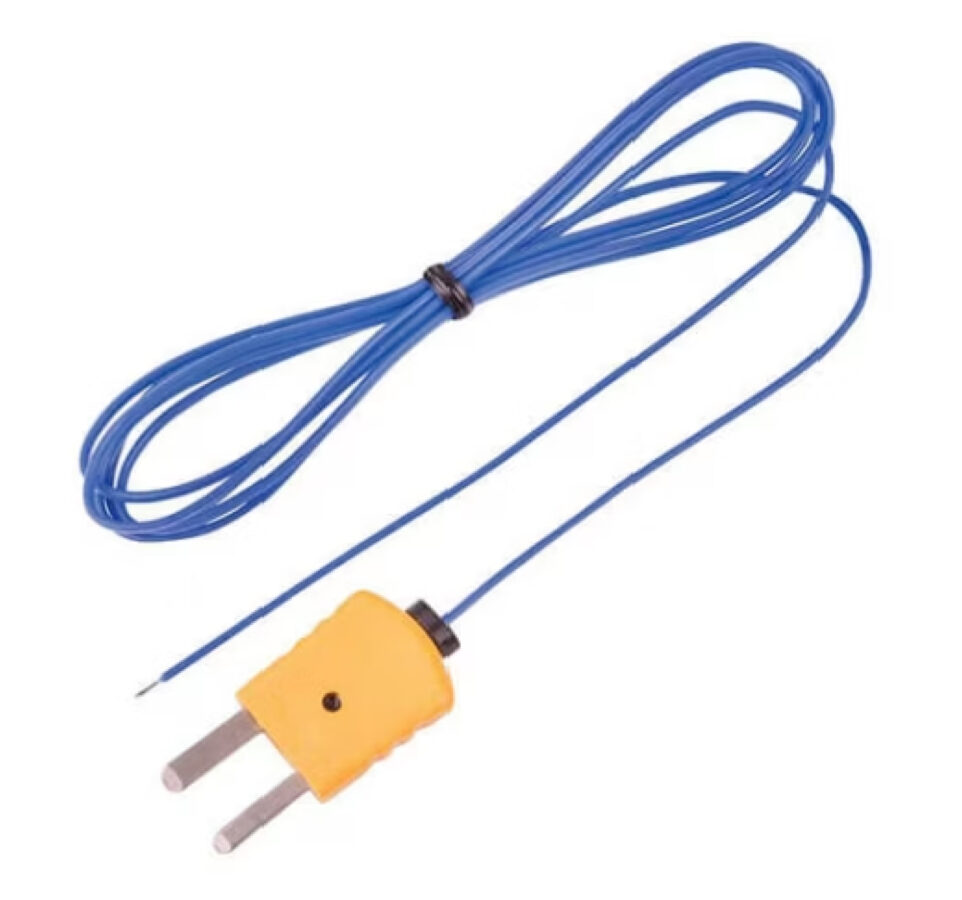
Thermocouples (TC)
Popular for their wide measurement range (-200 °C to ~1370 °C for Type K) and robustness. Compact, affordable, and suitable for harsh conditions, TC accuracy typically ranges from ±1 to ±2 °C and typically requires careful handling of cold junction compensation. Ideal for: High-temperature scenarios like engines, furnaces, or applications needing numerous cost-effective sensors..
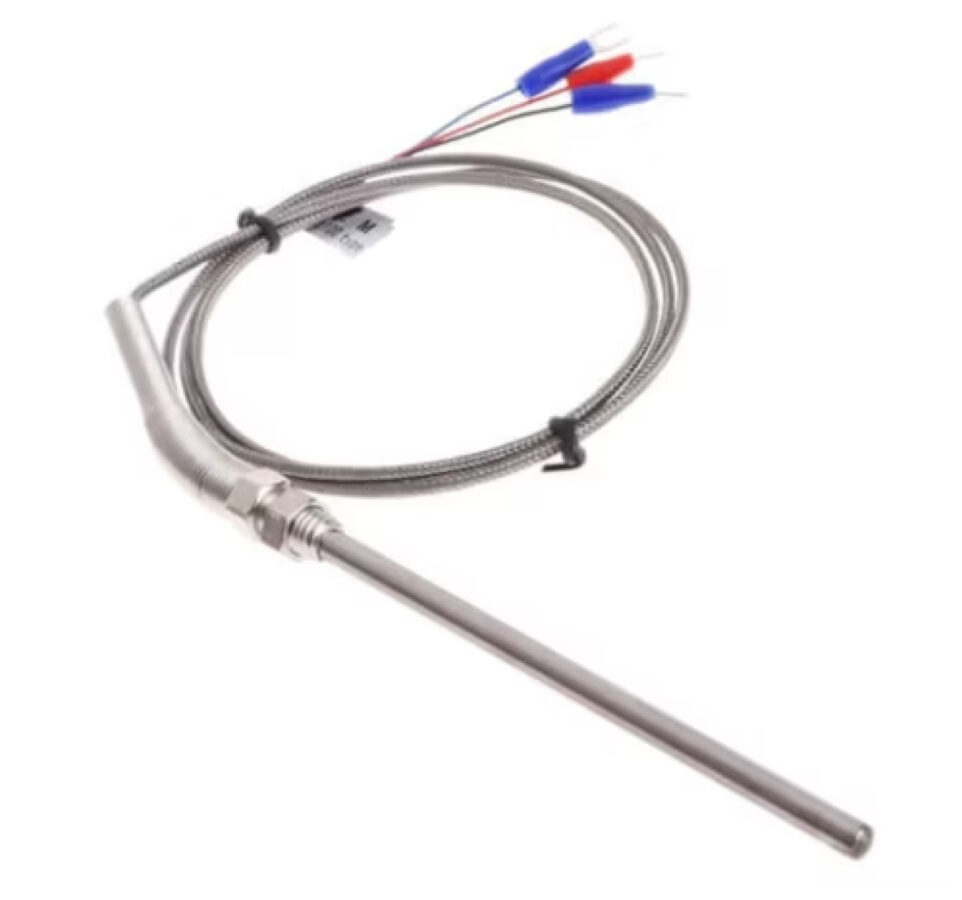
Resistance Temperature Detectors (RTDs - Pt100/Pt1000)
Known for exceptional accuracy (Class A RTDs offer ±0.15 °C accuracy at 0 °C) and stability over a moderate range (-200 °C to 600 °C). Although pricier and slower in response than TCs, RTDs offer excellent precision and consistent readings, ideal for industrial environments. Ideal for: Medium-range, precise industrial measurements such as environmental chambers, pipelines, reactors, or climate control systems.
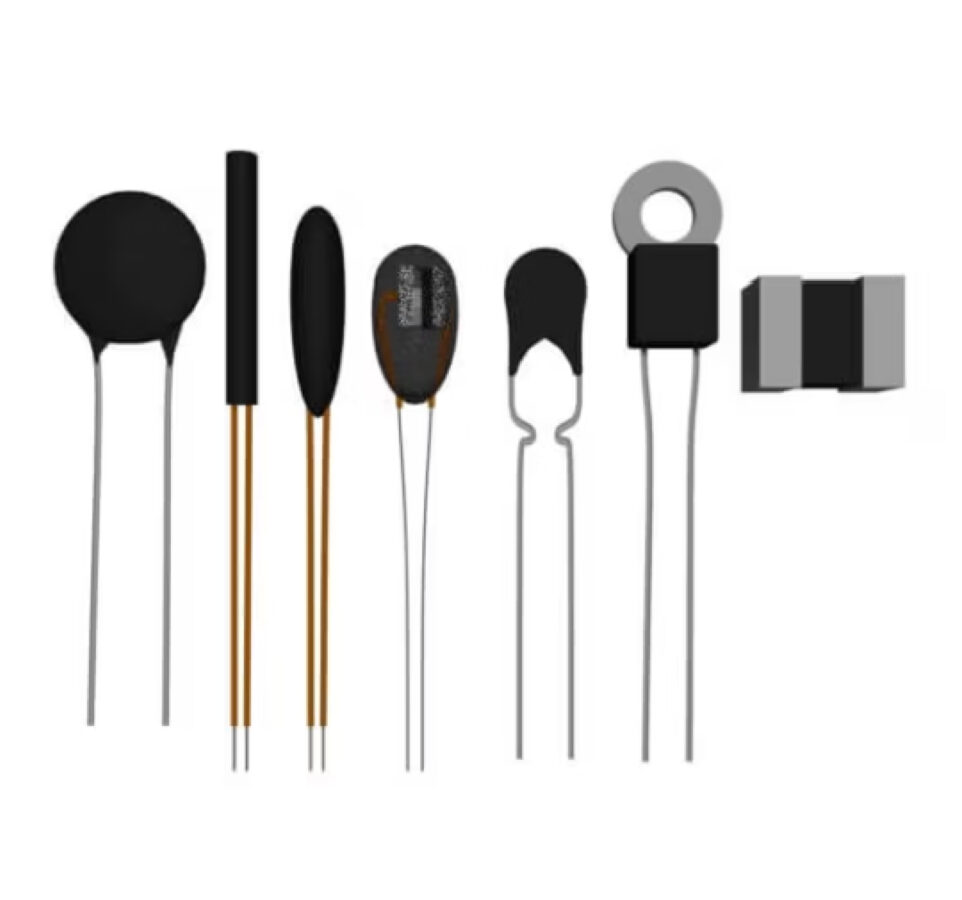
Thermistors (NTC)
Highly sensitive within narrow temperature ranges (typically -40 °C to 150 °C), offering high resolution up to ±0.1 °C. Economical and responsive, but being non-linear, require calibration or software linearization. Ideal for: Narrow-range, high-resolution applications like electronics temperature monitoring, battery packs, or medical devices.
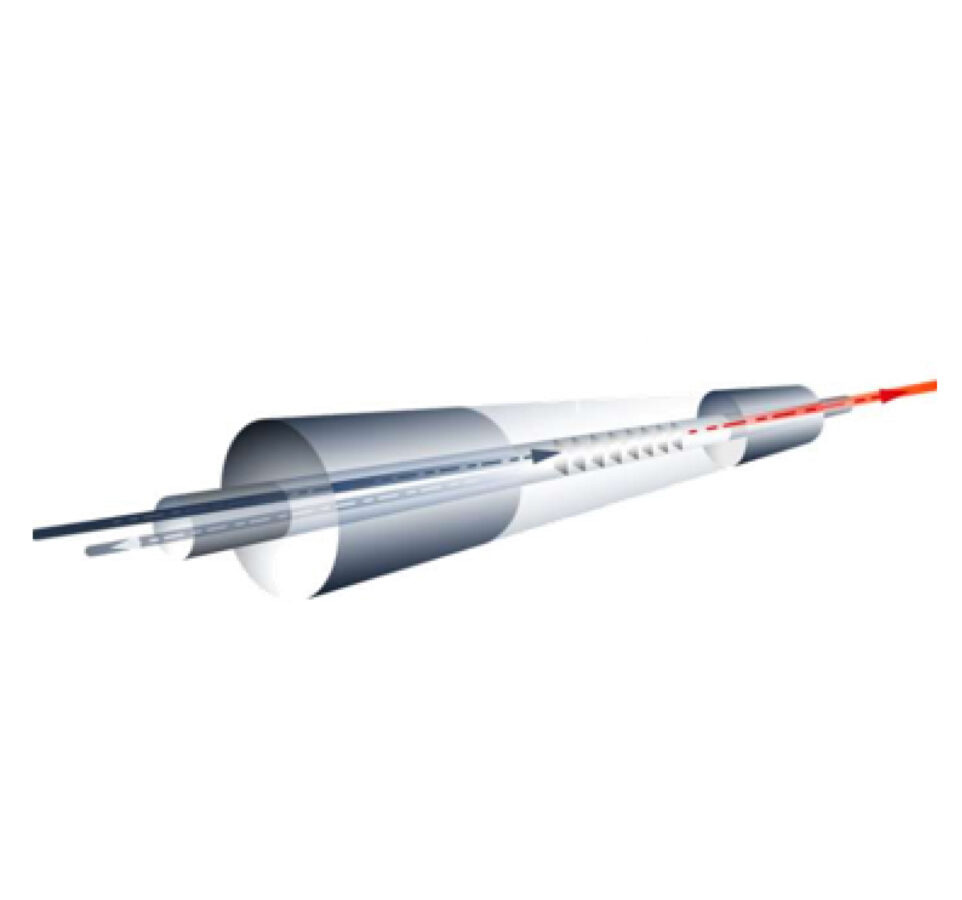
Fiber Optic Temperature Sensors
Essential for environments with high electromagnetic interference (EMI) or high-voltage conditions. These sensors offer electrical isolation and immunity to electromagnetic interference (EMI), making them suitable for specialized high-voltage or EMI-sensitive applications. Ideal for: Transformer and motor winding temperatures, MRI machines, and high-RF environments. (initial release: contact sales for integrated solutions)
What’s the Bottom Line?
- Thermocouples: Extreme temperature ranges, high durability, cost-effective for large quantities.
- RTDs: Industrial settings requiring moderate temperatures and high precision.
- Thermistors: Precise, localized measurements within narrow temperature ranges.
- Fiber Optics: Specialized, high-voltage, or EMI-sensitive environments (integrated solutions—contact sales).
Use our product finder to select the right measurement modules for your sensor type, or contact our experts for personalized guidance on selecting the appropriate temperature probe.
Achieving Accurate and Stable Readings
Obtaining precise temperature measurements with industrial temperature sensors requires addressing several common challenges:
Calibration and Tolerance
Solution: Standard Type K TCs (±2 °C) or Class B Pt100 RTDs (±0.3 °C at 0 °C) have defined tolerances. Select higher-grade sensors (Class A, 1/10 DIN) or calibrate sensor-instrument systems at known points to enhance accuracy.
Stability and Drift
Industrial temperature sensors drift due to contamination, mechanical stress, or aging. TCs exposed to high temperatures degrade, causing readings to shift over time.
Solution: Regular calibration of temperature sensors and operating them within recommended conditions can help reduce drift.
Repeatability and Noise
Fluctuations caused by electrical interference or poor sensor coupling result in unstable readings.
Solution: Ensure proper temperature probe installation, good thermal contact (e.g., using thermal paste or adequate immersion), and utilize instruments with digital filtering (e.g., Gantner DAQ modules’ 50/60 Hz rejection filters) to stabilize measurements.
Cold Junction Compensation (CJC)
Incorrectly handled cold junction compensation can cause significant errors (>10 °C).
Solution: Always use instrumentation with built-in, precise CJC (e.g., Gantner Instruments’ thermocouple modules).
Instrumentation Accuracy
Measurement devices themselves contribute to overall uncertainty. Even high-grade sensors perform poorly on low-quality loggers.
Solution: Confirm your instrument’s specifications match your accuracy requirements. High-precision instruments like Gantner’s Q.series modules minimize this error (resolution down to 0.01 °C, accuracy typically ±0.1 °C or better).
Effectively managing these factors — sensor choice, calibration, proper installation, and quality instrumentation — is crucial to ensuring accurate and stable temperature measurements.
Managing Thermocouple Reference Junctions
Thermocouples measure temperature differences, not absolute values, requiring accurate cold junction compensation (CJC). Ignoring proper CJC can cause large errors (tens of degrees).
Understanding the issue
A thermocouple measures temperature difference, not absolute temperature. The meter or module needs to know the reference junction temperature (usually the terminal temperature) to compute the actual temperature at the sensing end. If you neglect this, errors the size of the ambient variation will creep in (which could be tens of degrees).
Solutions
- Built-in Cold Junction Compensation: Built-in Cold Junction Compensation: Use DAQ modules with integrated temperature sensors (RTDs or thermistors) at terminal points. These automatically correct thermocouple voltage readings for variations in ambient temperature. Ensure your hardware is correctly set for your thermocouple type and verify internal CJC accuracy. Gantner modules include dedicated, highly accurate CJC circuitry.
- External Reference: External references, such as ice baths or stabilized chambers (maintained at 0°C), are highly accurate, but add complexity. They are typically employed in calibration laboratories. Built-in Cold Junction Compensation typically suffices.
- Terminal Stability: Ensure uniform temperature at terminal blocks to prevent variations or gradients (caused by drafts or hot electronics) that can lead to errors. Maintain stable ambient conditions or enclosures around terminals.
- Correct Connectors and Wires: Always use thermocouple-grade connectors and extension wires to prevent unintended junctions that could affect accuracy. Dissimilar metals create unintended junctions, which can affect accuracy. Industry-standard TC connectors (color-coded by type) prevent such issues.
Key takeaway
Properly managing cold junction compensation is essential for accurate thermocouple measurements. Built-in CJC (as provided by Gantner’s DAQ modules) simplifies setup and ensures reliability—when correctly configured, thermocouple readings remain stable and accurate.
Special Tip: External Cold Junction Compensation Board (CJC30)
For installations involving large channel counts or long thermocouple cables, Gantner Instruments offers the external CJC30 board, supporting up to 30 TC channels.
Equipped with an integrated Pt1000 sensor for precise measurement of the cold junction temperature, the CJC30 board serves as an isothermal reference junction, significantly reducing cable complexity.
RTDs Wiring Configurations – 2-Wire, 3-Wire, 4-Wire
When connecting RTD temperature sensors or thermistors, you’ll encounter options for 2, 3, or 4-wire connections. This is a common area of confusion, but it’s all about dealing with lead wire resistance:
2-Wire: The simplest method uses just two wires, but the measurement includes sensor and lead resistance, which can introduce significant errors—e.g., 10 m of thin wire (~1 Ω) adds approximately 2.6 °C error for a Pt100. Suitable only for short distances or lower accuracy requirements; thicker gauge wires reduce this error.
3-Wire: Most common in industrial applications, a third wire compensates for lead resistance by measuring and subtracting it, assuming equal lead lengths and gauge. This greatly reduces error—from about 2.6 °C to typically less than 0.2 °C—making it the standard compromise between complexity and accuracy.
4-Wire (Kelvin): Provides the highest accuracy by using separate pairs for current supply and voltage sensing, entirely eliminating lead resistance effects. Recommended for precision measurements, calibration, or very long cable runs. The downside is complexity and additional wiring cost. Match sensors and instrumentation for maximum benefit.
Thermocouples are inherently two-wire and don’t face these configuration choices because lead resistance has minimal impact due to high input impedance; the main concerns are noise and junction integrity.
Best practice:
Always opt for a 3-wire setup for RTDs to significantly improve measurement accuracy. Ensure correct wiring per your DAQ module’s manual, and use properly color-coded cables to maintain balanced resistances.
Did you know?
If you need modules that allow comprehensive temperature measurements using RTD, NTC, and TC sensors alongside other measurement parameters, such as voltage, strain, and vibration, then choose Gantner Instruments, which provides high-performance multifunction I/O modules for enhanced test flexibility and data integration.
A107: 4 Analog Input Channels
• Voltage: ±10 V, ±1 V, ±100 mV
• Current: Up to ±25 mA
• Resistance: 400 Ω to 4 kΩ
• RTDs: Pt100, Pt1000
• Strain Gages: ±2.5 mV/V, ±50 mV/V, ±500 mV/V
• Potentiometers: 1 kΩ to 10 kΩ
• Sampling Rate: Up to 20 kS/s per channel
A101: 2 Analog Input Channels
• Voltage: ±100 mV to ±10 V, 0–60 V
• Current: 4–20 mA loops
• Resistance: Up to 10 kΩ
• RTDs: Pt100, Pt1000
• Thermocouples: Types B, E, J, K, L, N, R, S, T, U
• Strain Gages: Full, half, and quarter-bridge configurations
• IEPE/ICP Sensors: For vibration and acoustic measurements
• Sampling Rate: Up to 100 kS/s per channel
Gantner Instruments is dedicated to helping customers transition smoothly to a sustainable future. We are happy to work with you to find the ideal data acquisition solution for your requirements!
Dealing with Electrical Noise and Interference
“My temperature readings fluctuate whenever the motor runs!”—a common frustration when measuring low-level signals such as thermocouples. Here’s how to ensure accurate, stable readings by minimizing electrical noise and interference:
- Use Shielded, Twisted-Pair Cables: Twisted pairs greatly reduce electromagnetic interference (EMI) by canceling magnetic field effects. Shielding further blocks external noise. Always ground the shield at one end only to avoid ground loops. TC and RTD sensor cables typically come pre-twisted; ensure this is standard practice.
- Separate Sensor and Power Cables: Keep low-level sensor wires physically separated from power lines, motor leads, and PWM cables to prevent interference. If crossing is unavoidable, do so at right angles. Consider metal conduit or cable trays as physical shields.
- Enable DAQ Filtering: Activate built-in filters on your measurement hardware. Low-pass or notch filters effectively reduce jitter and eliminate mains-frequency interference (50/60 Hz). Gantner modules offer selectable digital filtering to remove typical electrical noise, providing stable, clear readings. For slowly varying processes, software averaging can further smooth measurements.
- Check Your Grounding Strategy: Ground loops cause subtle yet significant errors. Use isolated, differential inputs (like those provided by Gantner DAQ modules) to prevent ground currents from interfering with your signals. If grounding issues persist, consider using ungrounded thermocouples or carefully grounding only one end of your system at the DAQ side.
- Proper Thermocouple Practices: Thermocouple signals are extremely small (in the microvolt range), making clean, secure connections vital. Loose or dirty connections can convert RF noise into measurable offsets. Many DAQ modules include built-in RC filters; if using general-purpose DAQ devices, consider adding small external RC filters (e.g., a 0.1 µF capacitor across inputs) to suppress high-frequency spikes.
- Identify and Mitigate Specific EMI Sources: Common interference sources include variable-frequency drives, welding equipment, and radio transmitters. Identify these sources by testing sensor performance with equipment both on and off. If EMI persists, additional shielding, re-routing, or filters may be required.
- Consider a Distributed DAQ Architecture: If noise persists despite these measures, consider shortening sensor cable runs by digitizing signals close to their source. Gantner’s distributed DAQ modules allow direct digitization at the sensor, significantly reducing noise susceptibility and ensuring robust signal transmission via fieldbus systems.
- Diagnose Using Frequency Analysis: If problems persist, perform an FFT analysis to identify specific interference frequencies. Many Gantner systems integrate seamlessly with analytical software, enabling precise identification and targeted filtering adjustments.
Following these best practices ensures reliable, stable temperature measurements—free from the interference that often compromises accuracy.
Measuring Temperature on High-Voltage Systems Safely
Accurately measuring temperature with industrial temperature sensors in high-voltage environments requires:
Use Isolated Measurement Modules
Select DAQ modules with high galvanic isolation (up to 1500 VDC).
Ensure Proper Sensor Insulation and Routing
Use sensors specifically rated for your voltage.
Avoid Grounded Sensors on HV Points
Choose ungrounded sensors to prevent ground loops.
Verify High Common-Mode Range Capability
Ensure your DAQ system handles high-voltage measurements.
Prioritize Safety with Expert Solutions
Follow expert solutions and safety protocols.Always follow proper safety protocols, including lock-out/tag-out procedures, when installing and operating sensors in high-voltage setups.
Why Gantner for Temperature Measurement?
With over 40 years of proven experience, Gantner Instruments provides accurate, stable, and reliable temperature measurement solutions trusted by leading organizations worldwide. Our versatile data acquisition (DAQ) hardware is specifically engineered for challenging temperature measurement scenarios, from precision thermocouple and RTD measurements to specialized solutions for high-voltage and cryogenic environments.
Whether using thermocouples, RTDs, thermistors, or fiber optics, Gantner Instruments delivers accuracy, stability, and robustness. Our DAQ modules ensure precise data acquisition, real-time analytics, and long-term reliability through:
- Intuitive software compatible with all OS platforms
- Powerful data archiving and intelligent data compression
- Exceptional long-term stability and low-noise performance
- Comprehensive, no-cost application support from experienced engineers
Gantner Instruments enables you to achieve precise temperature measurement results, overcome technical challenges, and exceed your testing and monitoring requirements:
- A104: High-precision thermocouple measurement
- A104 TCK – Standard miniature thermocouple measurement connectors optimized for Type K temperature probes.
- A104+ – Enhanced EMC-protected thermocouple measurement For thin TC wires or noisy environments
- A105: Versatile RTD (Pt100/Pt1000) and NTC measurement module
- A105 CR: Specialized low-current module for cryogenic measurements
- A105 10k: Dedicated NTC measurement module for extended resistance ranges
- A124: Thermocouple measurement module for high-voltage environments
- A121: High-voltage RTD and NTC measurement module
Typical Applications Include:
Mobility (electric vehicle battery testing), aerospace (engine and structural tests), energy systems (fuel cells, renewables), and civil engineering (infrastructure monitoring).
Discover how Gantner Instruments can tailor a robust, flexible temperature measurement solution for your specific needs.
Testimonials
FPT Fiat Powertrain Technologies – Heavy Duty Engines
Mahle Behr – Automotive Air Conditioning
Max-Planck-Institut for Plasma Physics – Nuclear Fusion Research
Schäffler Group
Safran Turbomeca – Turbo Engines
What our clients say
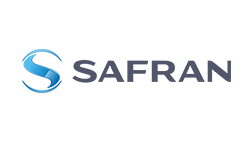
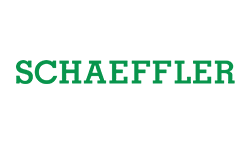
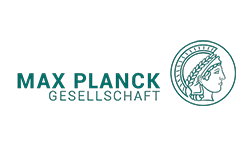
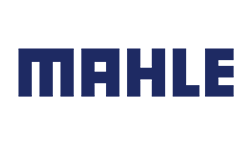
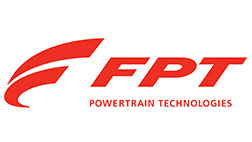
Application Examples
Gantner’s cutting-edge DAQ technology is trusted globally for applications in the mobility, aerospace, civil engineering, and energy sectors. Choose from the following industry examples to discover the most versatile DAQ on the market.
AE
Measuring temperature in components of Hybrid Electric Drives
Click here to request
access to every
GI Application Example
Get your All-Inclusive Gantner Instruments Battery, Fuel Cell & Electrolyzer Testing Flyer now!
Explore Our Temperature Measurement Products
Our online Product Finder can guide you to the appropriate modules based on sensor type and performance needs. Browse our comprehensive temperature measurement modules, optimized for diverse and demanding applications: